Industrial Engineering (IE):Industrial Engineering (IE) is a profession in which a knowledge of mathematical and natural sciences gained by study, experience and practice is applied with judgment to develop the ways to utilize economically the materials and other natural resources and focus of nature for the benefit of mankind. It is also known as systems engineering, production engineering, and operations management. Industrial engineering is going to play a pivotal role in increasing productivity. We have lots of article on Industrial Engineering (IE). Which links are given below.
A Comprehensive Study on Lean Manufacturing Process
Lean Manufacturing:
Lean Manufacturing – A way to eliminate waste and improve efficiency in a manufacturing environment. Lean focuses on flow, the value stream and eliminating ‘muda’, the Japanese word for waste. Lean manufacturing is the production of goods using less of everything compared to traditional mass production: less waste, human effort, manufacturing space, investment in tools, inventory, and engineering time to develop a new product. Lean is the systematic approach to identifying and eliminating waste through continuous improvement by flowing the product or service at the pull of your customer in pursuit of perfection.
Origin:
During II world war, the economic condition of Japan was heavily destroyed. They had limited infrastructure, inventories, machine & materials. So they decided to produce a small batch of products which would reduce inventories; it means they would need less capital to produce the same product. Lean manufacturing is a management philosophy derived mostly from the Toyota Production System(TPS) because Toyota Motor Company’s Eiji Toyoda and Taiichui Ohno are given credit for its approach and innovations, this system identified as "lean" only in the 1990s.
Procreation:
Lean was generated from the Just-in-time (JIT) philosophy of continuous and forced problem solving Just-in-time is supplying customers with exactly what they want when they want it With JIT, supplies and components are “pulled” through a system to arrive where they are needed when they are needed. Just in time (JIT) is a production strategy that strives to improve a business' return on investment by reducing in-process inventory and associated carrying costs. Just in time is a type of operations management approach which originated in Japan in the 1950s. It was adopted by Toyota and other Japanese manufacturing firms, with excellent results: Toyota and other companies that adopted the approach ended up raising productivity significantly.
Areas of Lean:
- Quality- Increasing quality.
- Cost- Reducing cost.
- Productivity- Increasing productivity.
- Safety and morale- Ensuring safety.
Waste elimination:
Waste is anything that happens to a product that does not add value from the customer’s perspective. Products being stored, inspected or delayed, products waiting in queues, and defective products do not add value. There are seven major types of waste –
- Overproduction – Producing more than the customer orders or producing too early. Inventory of any kind is usually wastage. TPS pays particular attention to the waste of overproduction.
- Queues – Time is a limited resource. In the manufacturing world, time is money. Customer requirements are calculated to the second. Idle time, storage, and waiting are wastes.
- Transportation – Moving material between plants, between work centers, and handling more than once is waste.
- Inventory – Preventing unnecessary inventory is critical to the success of the Toyota Production System. The smooth, continuous flow of work through each process ensures that excess amounts of inventory are minimized unnecessary raw material, work-in process (WIP), finished goods, and excess operating supplies are wastes.
- Motion –Motion is the movement of equipment or people. Wasted motion occupies time and energy. Ideally all unnecessary movements or actions are eliminated from the work process.
- Over-processing – It refers to the works performed on product that adds no value. Over processing is as wasteful as insufficient processing. Employees must learn to identify over processing waste.
- Defective product – The waste of correction is a result of poor internal quality. Producing defective products or products requiring repairs adds the cost of extra manpower, materials, facilities and conveyance measures.
Advantages of Lean Manufacturing:
- Increased overall productivity.
- Reduced amount of floor space required for production.
- Reduced manufacturing lead time.
- Improved flexibility to react to changes in production flow.
- Improved quality of the product.
Disadvantages of Lean Manufacturing:
- Difficulty involved with changing processes to implement lean principals.
- Long term commitment required for permanent change.
- Very risky process in case of supply chain issues while changing over to lean.
House of Lean:
As a business philosophy, Lean can be envisioned as a house. The House of Lean is formed by a foundation (Stability), two pillars (Just in Time and Jidoka), and a roof (Perfection). Many of the tactical components of Lean have been placed within these separate areas to give you a convenient frame of reference and an understanding of where certain tools fall within the vast arena of Lean.
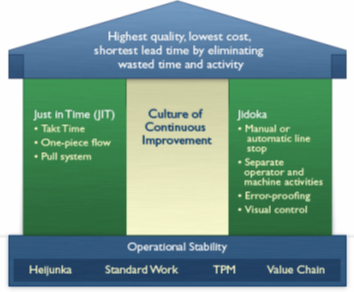
House of Lean
Role of Lean for Producers:
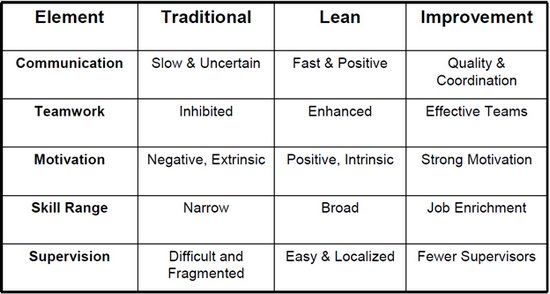
Role of Lean for Customers:
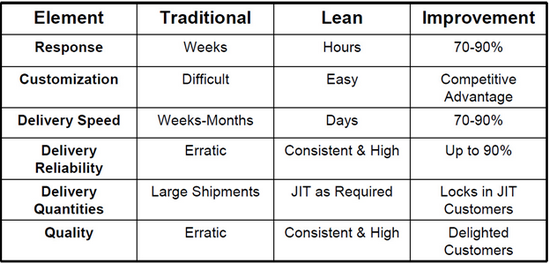
Lean Manufacturing Tools:
Lean manufacturing in a factory is maintained by several tools. The number and type of tool depends on the product that is to be produced and production system of the product. Most important tools are –
- 5S
- Andon
- Bottleneck Analysis
- Continuous Flow
- Gemba (The Real Place)
- Heijunka (Level Scheduling)
- Hoshin Kanri (Policy Deployment)
- Kanban (Pull System)
- Cellular manufacturing
- Jidoka (Autonomation)
- Just-In-Time (JIT)
- Kaizen (Continuous Improvement)
- KPI (Key Performance Indicator)
- Muda (Waste)
- Overall Equipment Effectiveness (OEE)
- PDCA (Plan, Do, Check, Act)
- Poka-Yoke (Error Proofing)
- Root Cause Analysis
- Single Minute Exchange of Die (SMED)
- Six Big Losses
- SMART Goals
- Standardized Work
- Takt Time
- Total Productive Maintenance (TPM)
- Value Stream Mapping
Lean Manufacturing Tools Suitable for Garments Factory :
- 5S- Strategy for creating a well-organized, smoothly flowing manufacturing process.
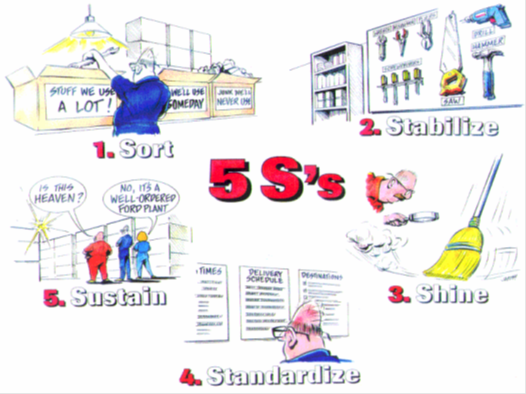
5S- system
- Cellular Manufacturing- Dividing the manufacture of products into semi-autonomous and multi-skilled teams known as work cells.
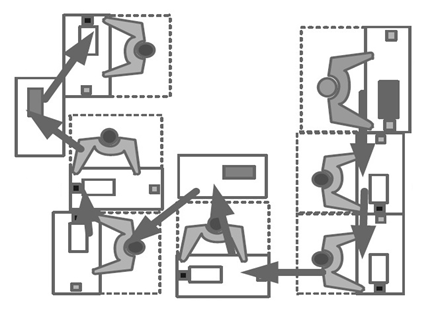
Cellular Manufacturing
- Kanban- A system that uses replenishment signals to simplify inventory management.
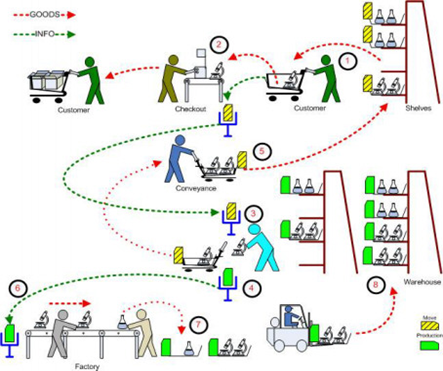
Kanban- system
References:
- www.lean.org
- en.wikipedia.org
- www.toyota-global.com
- www.toyota-forklifts.eu
- leanmanufacturingtools.org/
Lean Manufacturing:
Lean Manufacturing – A way to eliminate waste and improve efficiency in a manufacturing environment. Lean focuses on flow, the value stream and eliminating ‘muda’, the Japanese word for waste. Lean manufacturing is the production of goods using less of everything compared to traditional mass production: less waste, human effort, manufacturing space, investment in tools, inventory, and engineering time to develop a new product. Lean is the systematic approach to identifying and eliminating waste through continuous improvement by flowing the product or service at the pull of your customer in pursuit of perfection.
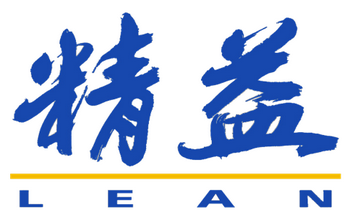
During II world war, the economic condition of Japan was heavily destroyed. They had limited infrastructure, inventories, machine & materials. So they decided to produce a small batch of products which would reduce inventories; it means they would need less capital to produce the same product. Lean manufacturing is a management philosophy derived mostly from the Toyota Production System(TPS) because Toyota Motor Company’s Eiji Toyoda and Taiichui Ohno are given credit for its approach and innovations, this system identified as "lean" only in the 1990s.
Procreation:
Lean was generated from the Just-in-time (JIT) philosophy of continuous and forced problem solving Just-in-time is supplying customers with exactly what they want when they want it With JIT, supplies and components are “pulled” through a system to arrive where they are needed when they are needed. Just in time (JIT) is a production strategy that strives to improve a business' return on investment by reducing in-process inventory and associated carrying costs. Just in time is a type of operations management approach which originated in Japan in the 1950s. It was adopted by Toyota and other Japanese manufacturing firms, with excellent results: Toyota and other companies that adopted the approach ended up raising productivity significantly.
Areas of Lean:
- Quality- Increasing quality.
- Cost- Reducing cost.
- Productivity- Increasing productivity.
- Safety and morale- Ensuring safety.
Waste is anything that happens to a product that does not add value from the customer’s perspective. Products being stored, inspected or delayed, products waiting in queues, and defective products do not add value. There are seven major types of waste –
- Overproduction – Producing more than the customer orders or producing too early. Inventory of any kind is usually wastage. TPS pays particular attention to the waste of overproduction.
- Queues – Time is a limited resource. In the manufacturing world, time is money. Customer requirements are calculated to the second. Idle time, storage, and waiting are wastes.
- Transportation – Moving material between plants, between work centers, and handling more than once is waste.
- Inventory – Preventing unnecessary inventory is critical to the success of the Toyota Production System. The smooth, continuous flow of work through each process ensures that excess amounts of inventory are minimized unnecessary raw material, work-in process (WIP), finished goods, and excess operating supplies are wastes.
- Motion –Motion is the movement of equipment or people. Wasted motion occupies time and energy. Ideally all unnecessary movements or actions are eliminated from the work process.
- Over-processing – It refers to the works performed on product that adds no value. Over processing is as wasteful as insufficient processing. Employees must learn to identify over processing waste.
- Defective product – The waste of correction is a result of poor internal quality. Producing defective products or products requiring repairs adds the cost of extra manpower, materials, facilities and conveyance measures.
- Increased overall productivity.
- Reduced amount of floor space required for production.
- Reduced manufacturing lead time.
- Improved flexibility to react to changes in production flow.
- Improved quality of the product.
- Difficulty involved with changing processes to implement lean principals.
- Long term commitment required for permanent change.
- Very risky process in case of supply chain issues while changing over to lean.
As a business philosophy, Lean can be envisioned as a house. The House of Lean is formed by a foundation (Stability), two pillars (Just in Time and Jidoka), and a roof (Perfection). Many of the tactical components of Lean have been placed within these separate areas to give you a convenient frame of reference and an understanding of where certain tools fall within the vast arena of Lean.
![]() |
House of Lean |
![]() |
![]() |
Lean manufacturing in a factory is maintained by several tools. The number and type of tool depends on the product that is to be produced and production system of the product. Most important tools are –
- 5S
- Andon
- Bottleneck Analysis
- Continuous Flow
- Gemba (The Real Place)
- Heijunka (Level Scheduling)
- Hoshin Kanri (Policy Deployment)
- Kanban (Pull System)
- Cellular manufacturing
- Jidoka (Autonomation)
- Just-In-Time (JIT)
- Kaizen (Continuous Improvement)
- KPI (Key Performance Indicator)
- Muda (Waste)
- Overall Equipment Effectiveness (OEE)
- PDCA (Plan, Do, Check, Act)
- Poka-Yoke (Error Proofing)
- Root Cause Analysis
- Single Minute Exchange of Die (SMED)
- Six Big Losses
- SMART Goals
- Standardized Work
- Takt Time
- Total Productive Maintenance (TPM)
- Value Stream Mapping
- 5S- Strategy for creating a well-organized, smoothly flowing manufacturing process.
![]() |
5S- system |
- Cellular Manufacturing- Dividing the manufacture of products into semi-autonomous and multi-skilled teams known as work cells.
![]() |
Cellular Manufacturing |
- Kanban- A system that uses replenishment signals to simplify inventory management.
![]() |
Kanban- system |
References:
- www.lean.org
- en.wikipedia.org
- www.toyota-global.com
- www.toyota-forklifts.eu
- leanmanufacturingtools.org/
Comments
Post a Comment