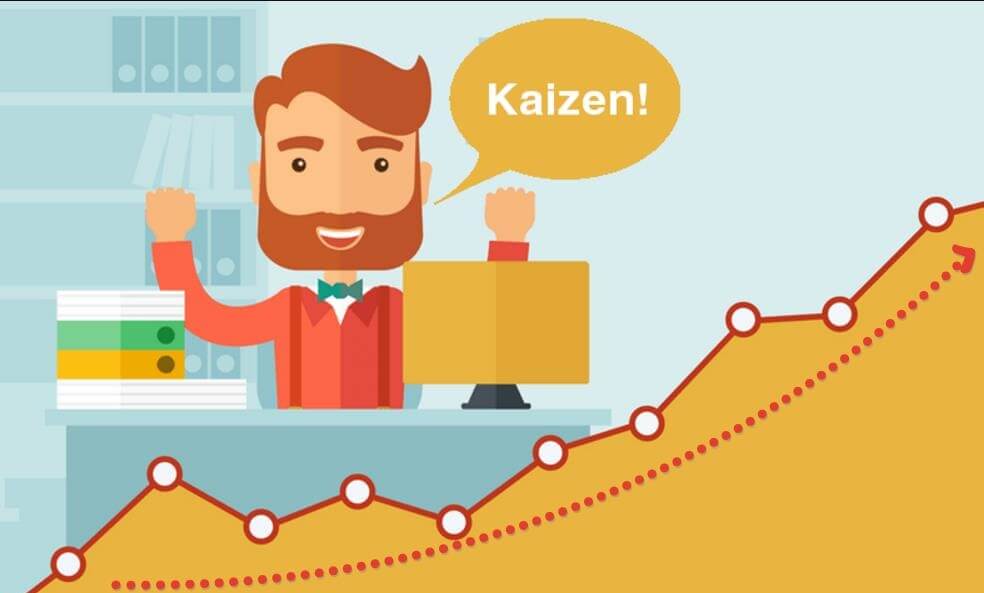
Kaizen nedir? Kaizen iyileştirmeleri nelerdir?
Kaizen kelimesi, Japonca değişim anlamına gelen “kai” ve iyileştirme anlamına gelen “zen” sözcüklerinden oluşur, bütünsel olarak düşünüldüğünde “iyileştirerek değiştirme” anlamını taşır. Herkesin gündelik hayatında sürekli uyguladığı küçük aksiyonlardır. Japonlar icat etmek yerine sürekli iyileştirme felsefesini benimsemiştir ve takım halinde hareket ederler, başarıya giden yolda, bir görevi birisini kahraman ilan ederek sadece o kişiye yüklemek yerine, görevleri takım halindeki gruplara paylaştırırlar. Bu yüzdendir ki Japon bir teknik adamın, tek başına kaldığında ne yapacağını bilemez bir halde etrafta dolaştığına dahi rastlanmıştır.
- Hızlı Kaizen
- Standard Kaizen
- Majör Kaizen
Bu kategoriler dışında majör kaizen kategorisindeki TIE (Toplam Endüstriyel Mühendislik) Kaizenleri ve İleri Kaizen yer alır. TIE kaizen’in majör kaizenden farkı iyileştirmenin kapsamında yer değiştirme yapılabilmesidir.
İleri Kaizen uygulamalarını yeşil kuşak ve siyah kuşak yalın uzmanları gerçekleştirmektedir, green belt ve black belt yalın eğitimleri farklı kurumlar tarafından belli periyodlarda tekrarlanmaktadır ve herhangi bir üretim hattında ileri kaizen proje ödeviyle tamamlanmaktadır.
1. Hızlı Kaizen: Kök sebep analizi gerektirmeyecek, hemen devreye alınabilecek, karmaşık olmayan, ekip lideri dahil en fazla 2 çalışma ekibi tarafından yapılabilecek, mevcut durumu fiziki değişiklik ile iyileştiren, kirlilik kaynağı, ulaşılması zor bölge kapsamında iyileşme sağlayan, öneri veya bir başka sürekli iyileştirme faaliyeti içerisinde yapılmamış olan, getirisi olan, işçi sağlığı ve iş güvenliği kapsamında iyileşme sağlayan, çevreye verilen zararı önleyen veya azaltan bir kaizen çeşitidir.
2. Standard Kaizen: Problem yaklaşımında araştırma ve veri toplama konularında metodik bir yaklaşım sağlar, kompleks arada bir olan problemlerin çözülmesinde kullanılan bir araçtır. Orta seviye iyileştirmelerde etkin olarak kullanılır ve genellikle 3-4 kişinin katılımıyla gerçekleşir. Fenomenin ortaya çıkarılmasını ve kök sebep analizinin yapılmasını, kök sebebi bulunarak alınan karşı önlemlerin etkinliğinin proseste doğrulanmasını ve elde edilen sonuçların sürekliliğini sağlar.
3. Majör Kaizen: Kompleks ve kronik problemlerin çözümünde daha uzun sürede ve daha fazla katılımcıyla uygulanan bir araçtır. Ekip 3 – 7 kişi olabilir ancak üye sayısının fazla olması tercih edilir. Teknik uzmanlık gerektirir. Daha detaylı analizlerin yapıldığı ve / veya daha fazla prosesi içeren bir çalışmadır. Çalışma her bir adımın ayrı ayrı görülebileceği görsel bir şekilde kayıt altına alınır. Ekip lideri problem çözme adımlarına uyumu sağlar. Ofis / satış / pazarlama bölümünden katılanlar (kendileriyle ilgili olan yerlerde) çalışmaya farklı bir bakış açısıyla katkıda bulunabilirler. Bu yazıda üretimde iyileştirilebilir fonksiyonlardan 3 tanesini inceleyeceğiz:
- İsraflar ve kayıplar
- Üretim esnasında yaşanan düzensizlikler
- Ergonomik problemler
Bunların dışında, profesyonel ve otonom bakım iyileştirmeleri, kalite iyileştirmeleri, personel iyileştirmeleri, lojistik iyileştirmeleri, çevre ve enerji ile ilgili iyileştirmeler, ürünlerin birim maliyetlerinde yapılan iyileştirmeler, iş sağlığı ve güvenliğini ilgilendiren konularda iyileştirmeler, ürün devreye alma sırasında yapılan iyileştirmeler de firmalarda uygulanabilmektedir.
İsraflar ve kayıplar yalın dilinde MUDA, düzensizlikler MURA, ergonomik sorunlar ise MURI olarak adlandırılır. Bu üçünde de ortak amaç üretim süresini ve kalitesini iyileştirmek ve firmaya iyileştirme yapılan hat üzerinden kar ettirmektir.
1. MUDA: Müşteri istekleri adına değer yaratmayan her şeye muda denir. Değer ise müşterinin beklentileri ile maksimum seviyede örtüşen ürün ve/veya hizmettir. Bir iş yerinde 8 temel muda vardır:
- Fazla üretim
- Stok
- Taşıma
- Hareket (Yürüme)
- Bekleme
- Düzeltme (Yeniden işlem yapma)
- İşleme (Üretim esnasında gereksiz işlem)
- Çalışanların yeteneklerinden faydalanamamak
2. MURA: Bir operasyonda operatörlerin acele etmesine ya da beklemesine neden olan, nihai tüketici talebinden değil, üretim sistemi veya düzgün olmayan çalışma hızından kaynaklanan sürekli değişen üretim planıdır. Devamlı değişen üretim planları ve müşteri taleplerindeki dalgalanmaların kompanze edilememesine ve çalışma alanındaki işi engelleyen ve zorlaştıran her türlü düzensizliğe mura denir.
Düzensizliklerin ortadan kaldırılması için; analizi yapılacak operasyonda çalışan her vardiyanın asil operatörlerine ardışık en az 30 adet parça yaptırılarak her parçanın üretim süresi kayıt edilir ve buna müteakiben ayrı ayrı her operatörün parça zamanları analiz edilir. Ardından düzensizliği en az olan ve en iyi sürede üretim yapan operatörün yaptığı parça süreleri incelenir ve süre analizinde anormal değişkenliklerin olası nedenleri belirlenir. Son olarak; tespit edilen anormallikler operatöre eğitim verilerek anlatılır ve ilgili operatörün düzensiz sürelerde üretim yapması ortadan kaldırılmaya çalışılır ve aynı eğitim diğer operatörlere de verilerek operatörler arası düzensizliğin yok edilmesi sağlanır.
3. MURI: Bir işletmede çalışan operatör, makine veya diğer birimlerin gereğinden fazla yüklenerek ideal zaman ve emek miktarının üzerinde zorlanmasına muri denir. Yorgunluğa sebep olan operasyonlara örnek olarak; kas yorgunluğu, kötü çalışma pozisyonu kaynaklı yorgunluk, zihinsel ve duygusal yorgunluk gösterilebilir.
İyileştirmeler bu fonksiyonların birinde ya da hepsinde aynı anda yapılabilir, iyileştirme yapıldıktan sonra ürün birim maliyeti ve üretim süresinden edilen kâr çıktılarıyla; iyileştirme projesinin getirdiği karı, iyileştirme proje maliyetine oranlayarak bir B/C (Benefit/Cost) oranı buluruz, üst yönetime yapılan iyileştirme proje sunumunda bu veri önemli bir yer tutar. Yalın çalışmalarda önemli olan üst yönetimin desteğine ek olarak, yalıncıların bu desteği oluşturmaya yönelik yaptığı analiz çalışmaları ve bu mühendislik çalışmalarının çıktılarıyla üst yönetimi ikna edebilmeleridir.
Comments
Post a Comment